Metal casting is a demanding practice that requires strict attention to detail. After all, cast parts are components in various essential industries. When casting quality fails to meet specific criteria, other systems may not operate efficiently. Here at Warner Brothers Foundry Company, we go above and beyond to ensure our products live up to non-ferrous metal standards.
How We Ensure Casting Quality
There’s more to quality assurance than meets the eye — literally. Our manufacturers look beyond physical appearances, testing structural integrity, chemical composition and dimension variations. We focus on four primary areas when testing quality standards for castings.
Degrees of Soundness
Degrees of soundness refer to the visual aspect of metal casting inspections. During this process, we ensure the surface is free from cracks, porosity and other surface-level imperfections. We also check castings for bends or distortions.
Mechanical Properties
Once the surface is up to standard, we move on to testing the mechanical properties, such as strength and ductility. More specifically, we focus on grain size and shape, dendrite-arm spacing, and size and distribution of second-phase particles and inclusions. These features affect the overall strength and durability of metal casting.
Tolerance
Tolerance is an industry term referring to deviations from the specified physical dimensions of a component. During our tolerance inspections, we determine whether any dimensional variations impact the component’s function. Tolerance testing is an essential part of quality assurance, as it identifies possible errors in the part before it gets to the next manufacturing stage.
Chemical Properties
We use Spark Atomic Emission Spectrometry to test the chemical composition of the metal, ensuring the part meets aluminum alloy standards.
Premium-Quality Castings
The production of “premium-quality” castings is an example of understanding and using the solidification process to a good advantage. In the production of premium-quality castings, composite molds combining several mold materials are used to take advantage of the special properties of each casting process. High mechanical properties in designated areas are obtained by the use of special chills, Plaster sections and risers may be used to extend the feeding range of the casting.
Premium-quality castings are made to the tight radiographic and mechanical specifications required for aerospace and other critical applications. Basic linear tolerances of + 15 mils/in. are possible with aluminum alloy castings, depending on mold material, equipment, and available fixtures, and a minimum wall thickness of 3.8 mm (0.15 in.) is typical. Aluminum alloys commonly poured as premium-quality castings include C355, A356, and A357.
- Federal QQ
- QQ-A-601
- QQ-C-390
- ASTM
- B26/B26M – 14
- B584-14
- B148-86
- SAE AMS-STD-2175
- MIL-STD-2175
- MIL-C-6021
- MIL-A-21180
- Conflict of Materials
- Test Bars
- Material Certification
- AS9100 and ISO 9001 Compliance Certification
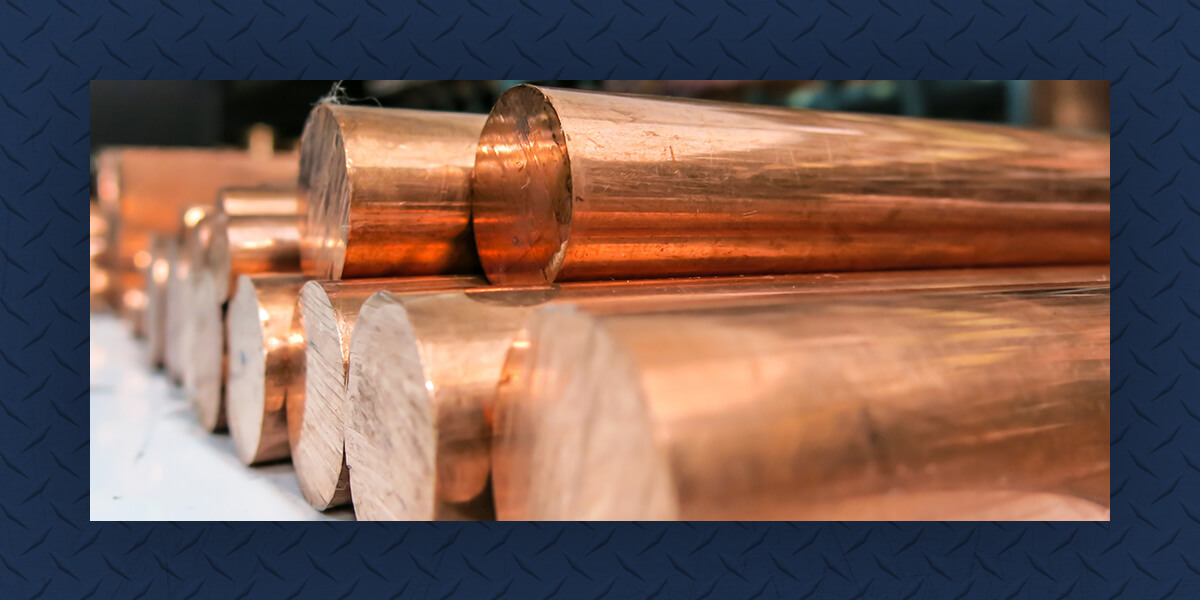
The Importance of Quality Assurance
Metal casting quality standards exist for a reason. Components that meet or exceed these standards are also likely to deliver in these key areas:
- Safety requirements: Structural integrity, chemical composition, strength and tolerance play essential roles in ensuring a metal component is safe to use. For instance, cracks or holes in a metal container could allow a toxic or flammable gas to escape, putting everyone nearby at risk.
- Industry standards: Drastic project delays occur when metal components fail to meet industry standards. We save you time by getting the details right.
- Consistency: Consistent quality is essential for mass manufacturing projects. It’s vital that each component has the same tolerance and quality.
We Can Help You Meet Metal Casting Quality Standards
At Warner Brothers Foundry Company, there is nothing more important than providing quality metal casting. We pride ourselves on precision and accuracy, ensuring each product meets industry standards. Contact us online to request a quote and benefit from our quality metal casting services.